首先哈,压铸这个东西,属于金属热加工工艺的一部分,所以谈这个东西的技术点,你首先至至少得对金属热加工工艺,或者热加工工艺
稍微有点点了解。
鄙人不材,之前玩塑料注塑工艺的时候顺路了解过一些压铸工艺,最近又找几个老头好好聊了下这玩意,恰好又能锤一些不学无术的群体,非常快乐。
科普长文预警,如果你真的希望学到什么东西,这可能是这个问题下面少数有用的回答。
这篇文章的核心,其实除了讲技术原理以外,还希望各位认知工业级设备的时候不要用消费级设备去随意理解,你们拿到手的消费产品,比如一个可以超频的CPU,你如何使用它,宣传他,和工业体系与自动化生产是截然不同的概念。
随意类比很容易引喻失义,希望注意。
从注塑讲起
注塑的产品大家估计都见过,大到一些低端车的车门内饰板,小到一个脸盆一根牙线,都是注塑出来的东西。
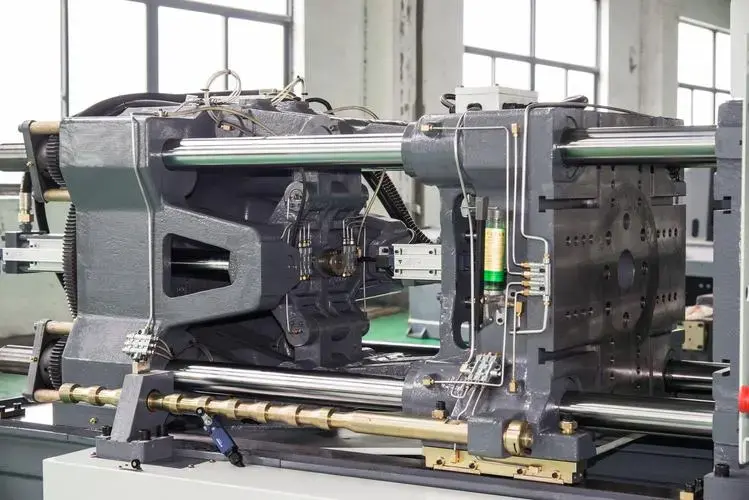
他原理很简单,一边是一个加热锅,把塑料颗粒加热融化,一边是一个大的模具和大的压力设备,chua!的一下,融化的塑料就被挤到模具里面,冷却了挤出来,就是一个产品了。
在中国市场,注塑产品一年的规模大概在6-7000亿人民币左右。换句话说,你要觉得注塑很简单,你懂注塑,你行你上。
而注塑本身呢,说简单,其实真的很简单,你有五千块钱,就可以去东莞找个注塑厂开个小模具,直接kuakua开始生产,至于生产出来什么牛鬼蛇神,你先别管。
粗糙的注塑制品想必大家都看过,一元店里粗糙的各类夹子,小工具,小学门口一块钱一包的玩具,都是非常常见的粗糙注塑制品。
但是,一个航空尼龙垫圈,也是注塑出来的,大批量下单品成本不过几毛钱,可以用在飞机重要结构上。
我不知道你们小时候有没有买过拼装的塑料模型,贵的有田宫的,威龙的,便宜的有三角号手,甚至更加不知名的厂商的产品,我记得我小时候拼一条1:350的三角号手提康德罗加级巡洋舰,那么大一个盒子,那么大的一条船,还带电动机,带金属轴和齿轮箱,放在水里嘎嘎跑的,他在05年左右线下店里,卖25块人民币一盒
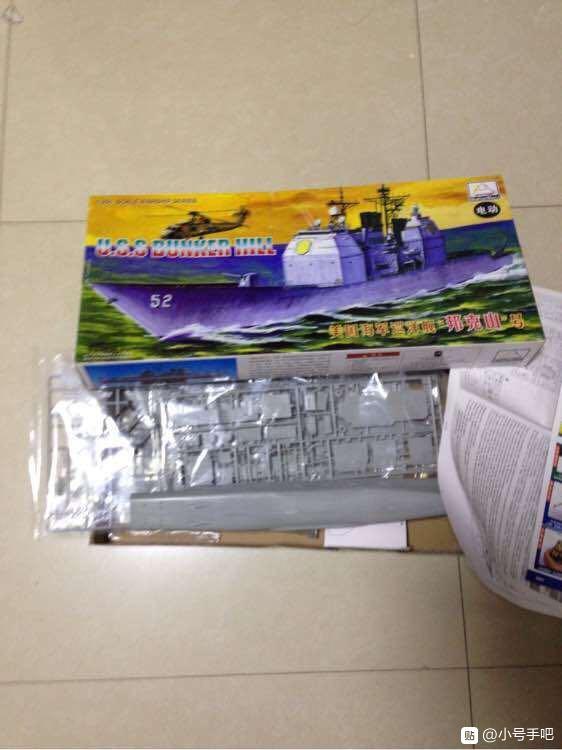
就是图里这玩意,那时候我还买过同级的邦克山号,也是25元一条。那时学校门口的手抓饼3块钱,一碗凉粉5毛钱,一瓶可乐2块5毛钱,也就是说当年10瓶可乐就可以买到一盒超大的1:350塑料拼装模型,装上电池可以在水里嘎嘎跑,连雷达杆子都一清二楚的仿真模型。
拼好之后,大概张这个样子
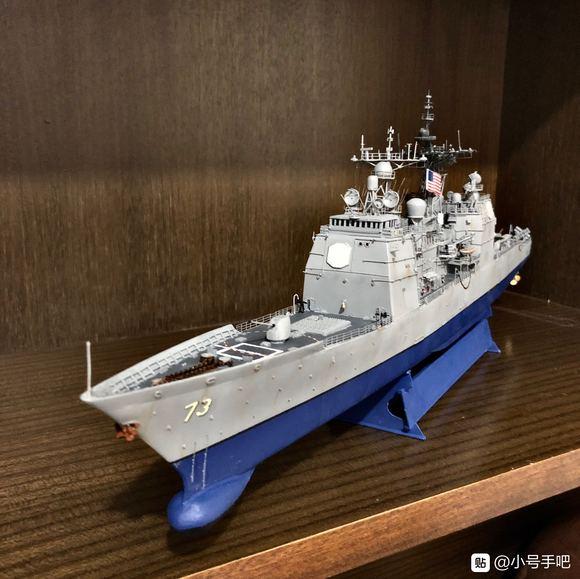
当然我必须要说,这个一看就是做了改进的,包括栏杆都是自己做的,桅杆上的栏杆,张线,涂装都是作者自己做的。
那时候我以为整个世界上最好玩的塑胶模型就是这样的,我在我小学的时候拼了差不多二十条三角号手各式各样的模型,因为那时候周练我只要全班第一,我妈就会带我去少年宫隔壁的玩具市场买玩具回来拼。
直到我在5年级的时候,家里亲戚看到我拼的一个舰队,或许觉得海军才是马鹿,于是给我买了一个港龙(威龙)的虎式模型。
这个模型的组合度,精细度,每一个零件的质量,甚至包括拼接履带的细节,都让我大惊失色,原来同样是注塑,可以到完全不同的两个水平。
再到后面,初中接触到了田宫的1:350 大和,又一次惊为天人。
那时的我还不懂工业,只认为这是一分钱一分货的表现,贵这么多,肯定质量好很多嘛。
那时候拼25块的三角号手,家里除了水口钳之外,还要常备砂纸,胶水,因为那个注塑的小板子会有各种小问题,需要我手动解决。
这里我就按照注塑的一些行业基本常识来罗列一下
色差:
都是最基本的问题,两块板子颜色都可能有轻微差异。
注塑不饱满:
一些特定零件凹下去一点,或者他的末端细小的部分和说明书上画的不一样,残缺了,比如桅杆一些地方。
变形:
一些比较长比较细的零件,在板子上就是弯曲的,你得手动掰回来。
熔接痕:
一些柱状比较长的零件,如果两边都有进胶的点位,那中间部分可能就会有两坨塑胶熔合在一起但是又没完全在一起的波浪形或者曲线的痕迹。
波纹:
一些大面积的平面零件表面的雾状或者波浪凹凸的纹路,在透明的比如窗户的零件有的会有水波纹。
飞边(披风):
一些零件的边缘有非常非常薄的一层感觉是长出来的小刀片一样的东西,边缘一般是波浪形的,是塑胶注塑的时候从缝隙里溢出来了。
银丝:
一些比较长的零件上会有,很长的白霜一样的细纹,沿着注胶口往末端延伸的方向。
脱模弯曲:
在脱模的顶针附近的弯曲,变形。
尺寸变形:
有些零件就是小一号,他缩了。
气泡:
有的零件表面有一个小凹坑,其实是气泡在表面,有的零件切开后一个洞,就是气泡在里面。
浑浊:
有的零件半透明本来均匀的,结果一看发现不平整,没光,或者发白,发雾
冷料:
就是加热的塑料和没加热的其实色泽,性能会有差异,混在一起。
白点:
一些透明的注塑件里面有一些白色的颗粒,不是气泡,实心的。
.......
等等等等,一堆一堆的。
那么如何解决这些问题呢?在注塑行业有一些通行的做法,你可以叫标准答案,就是教科书上教的,实际操作中往往比这些复杂,也更杂糅,多个问题多个因素并行
色差:
最基本的问题,可能是原料色粉混的不均匀,定型剂有问题,或者混料本身的色差,或者加工的温度,压力,熔胶时间的差异,甚至同一工厂不同的机台做的都可能有差异。
注塑不饱满:
模具设计的不好,一些很深,很细,很长的东西,或者特别薄(薄壁),或者离浇口很远的地方,就会出现不饱满,也有可能是浇口位置没设计好,没平行设计,或者浇口不在厚壁位置,也有可能是模具排气出了问题,或者注塑过程中融化的塑料有杂质,也有可能是模具或者注塑的塑胶温度不够,或者塑胶湿度太高了(之前就有工厂遇到这个问题,春天夏天注塑总出问题),或者原材料里杂质,或者再生料比例太高了,或者注塑机的压力,注射量不够,或者喷嘴孔太小,或者料筒供应有问题,或者止逆阀炸了,或者注塑行程不够,或者模具温度不对,或者注射压力太低等等
变形:
可能是注塑的压力不对导致流体不同流向的塑胶分子取向有差异,收缩不对了,或者回火的温度太高了,或者回火时间长了,或者保压时间不对,或者注塑速度太慢了或者太快了,或者塑胶温度太低了。
熔接痕:
进胶口太多了,进胶的截面太小了,冷料处理不正确,模具冷却不正确,模具温度不正确,脱模材料配比不对,胶的配比有问题太粘稠了,或者还是胶太潮湿了,或者塑胶熔化的温度太低了,分流汇合性能差,注射压力过低了,注塑速度太慢了,温度有差异。
波纹:
冷料处理不正确,冷料穴没设计好,塑胶流动性过低,改性材料性质不明确。
飞边(披风):
模具没修好啦,赶紧让师傅去打铜公啦!(笑
帕拉面不对啦,太粗糙了,型腔有问题啦,胶不对啦,胶温度太高了啦,胶注塑速度太快了啦,胶的压力不均匀,冲模速度不对啦,注射时间太长了,保压太久了,注射量太大了,一次给多了胶。
银丝:
原材料不行,可能是湿度大,水分大,没有提前烘干,或者是塑胶里回收料太多了,或者是你用的脱模剂不太对,挥发了不少。或者你的注塑温度太高,在高温下停留时间太长,或者塑胶在模具内保压保温时间太长,或者注塑速度太快了。
脱模弯曲:
模具没设计好啦,让师傅去打铜公都没用啦!(笑
顶针设计好了嘛?四行位模具也不好搞啦,脱模剂有问题,或者塑胶太软,或者注塑压力过大,或者塑胶的温度过高,或者塑胶粘性太强,或者塑胶件有飞边脱模刮到了,或者喷嘴温度太低了,或者冷却时间太短了,或者注塑时间太长了,或者保压时间太长了
尺寸变形:
混料没混好,收缩率不同的东西混进去了,模具也没对应设计好,或者注射压力太小,注射压力太大,冲模时间太短,保压时间太短,或者模温有问题,太低了。
气泡:
含水量太多了,没烘干,或者烘干温度太低了,原材料也可能不对,收缩率太高,或者回收料太多,或者注射速度太快,时间太短,气体没跑掉,或者保压时间太短,或者冷却没设计好,冷却不均匀,或者冷却时间不够,或者塑胶的温度和模具温度太高了,塑胶里面东西都挥发了。
浑浊:
原材料还是含水太多了,易挥发物太多了,润滑剂太多了,塑化温度太高了,注射速度太快了,塑胶的温度太高了,注射压力太大了。
冷料:
胶料韧性太强了,脱模后水口会拉丝还会黏住,胶的温度太低,塑化有问题,模具问题太低,胶的流动性有问题。
白点:
原材料不对,颗粒不均匀,融化不均匀,来料有杂质,不能熔合,或者透明料太多了,或者料筒温度太低了,或者螺杆挤压的太快了,注塑时间太短了,或者压力太低了。
.....
压铸和大压铸
我不知道看这篇文章的人有没有学过金属热加工的,我想看到上面一些名词,你们会感到非常非常非常熟悉,甚至感觉就是类似的甚至一模一样的操作,类似的甚至一模一样的问题。
某种程度上来说,塑胶注塑和金属压铸真的有点像,只不过后者规模大的多,强度高的多,从速度到压力到成型的复杂度都要比前者更恐怖。
正如前面所说,注塑行业在中国是6-7000亿的市场,大家用的注塑机大同小异,你要是懂注塑,能玩好这些机台,你成为中国首富指日可待,请。
好,回到压铸
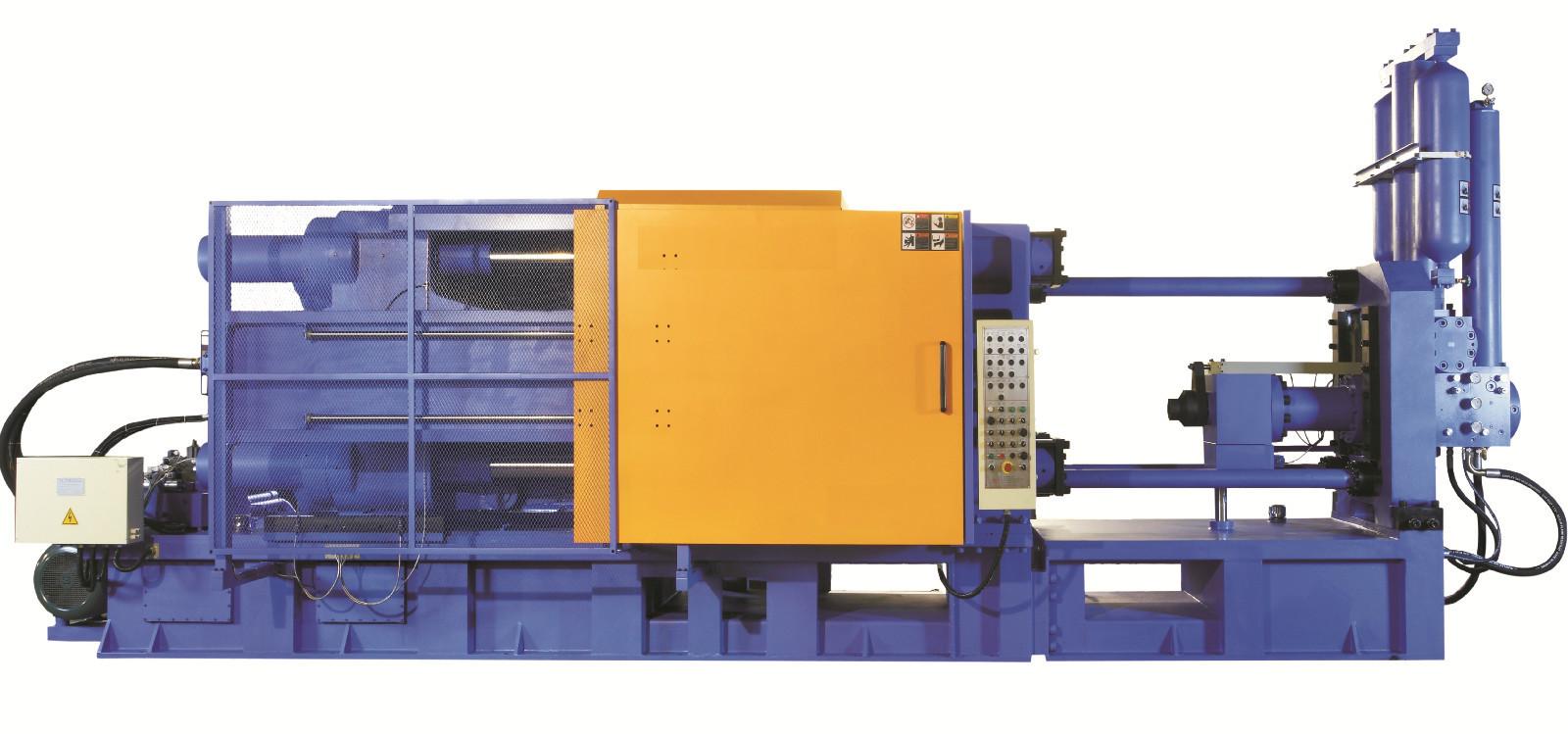
这是一台典型的冷室压铸机。
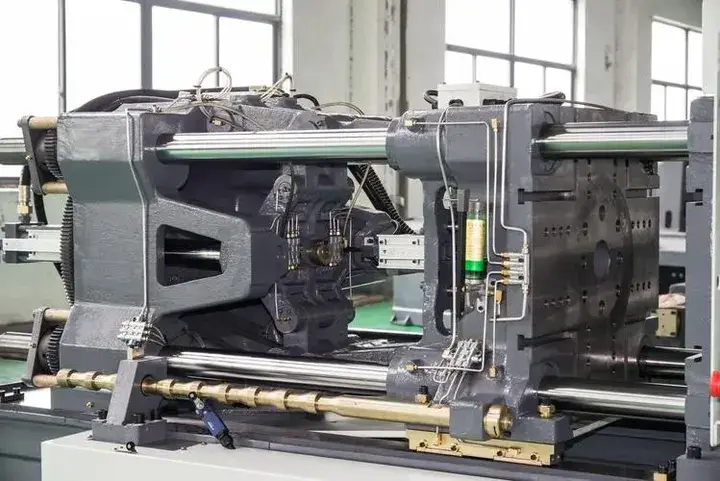
这是一台注塑机。
是不是太像了。
只不过前者真的要复杂很多,一台注塑机配合一个工人一个机械臂就能完成从上料到出货的操作,但是压铸机的自动化生产线,需要一整个压铸岛。
而压铸本身的原理,并不难,高温熔融的金属,一般是镁合金,铝合金这种东西,chua的一下,通过超大压力射到模具里面,冷却成型,出来就好了嘛~
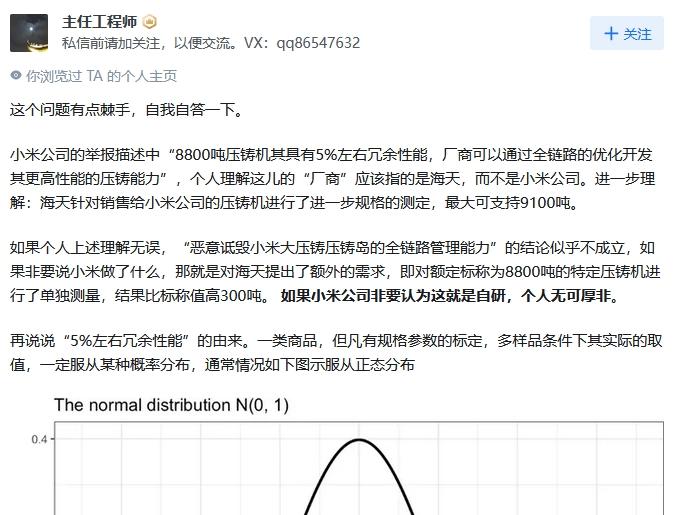
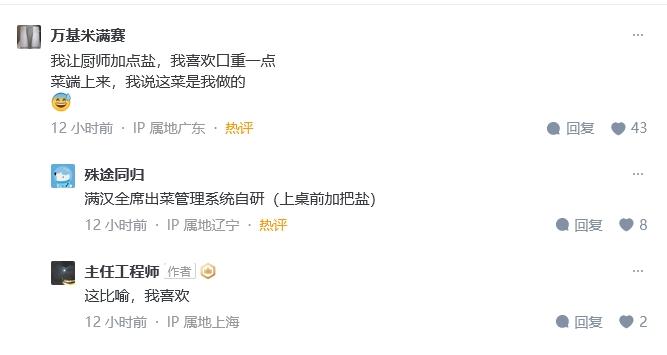
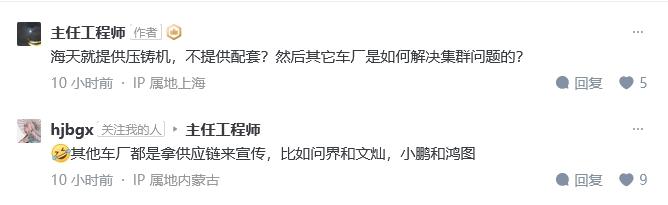
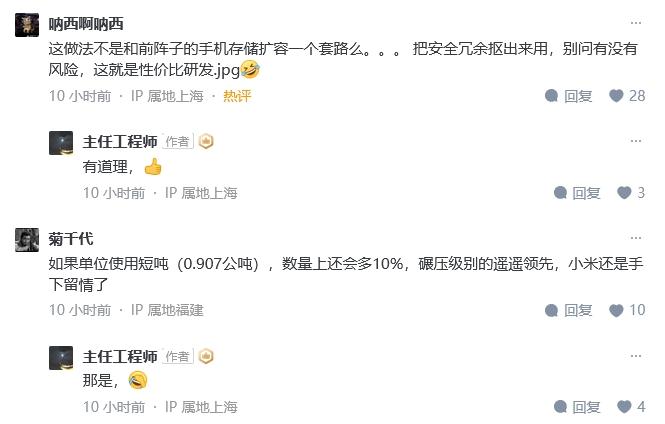
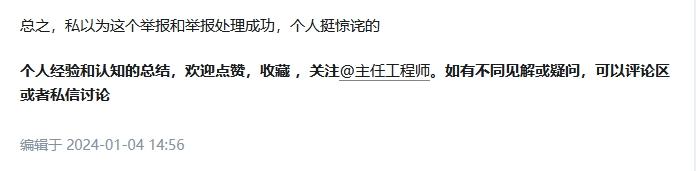
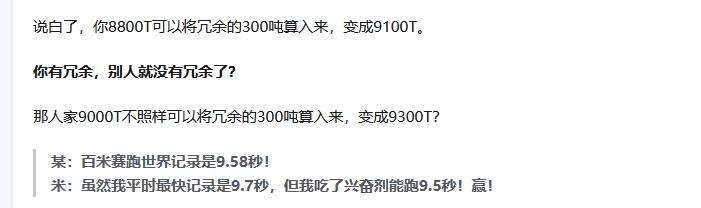
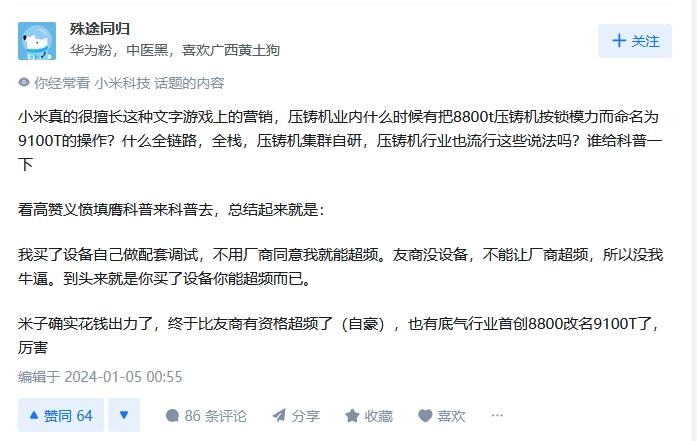
很简单的,中国铝压铸行业一年产值接近2000亿人民币,想必图例这些一夜成神压铸仙人们一定能凭借自己的实力在压铸行业分一杯羹吧?
好,不开玩笑了,继续讲压铸,如果要把压铸流程简单化,这里用东芝压铸机的培训资料来用一用

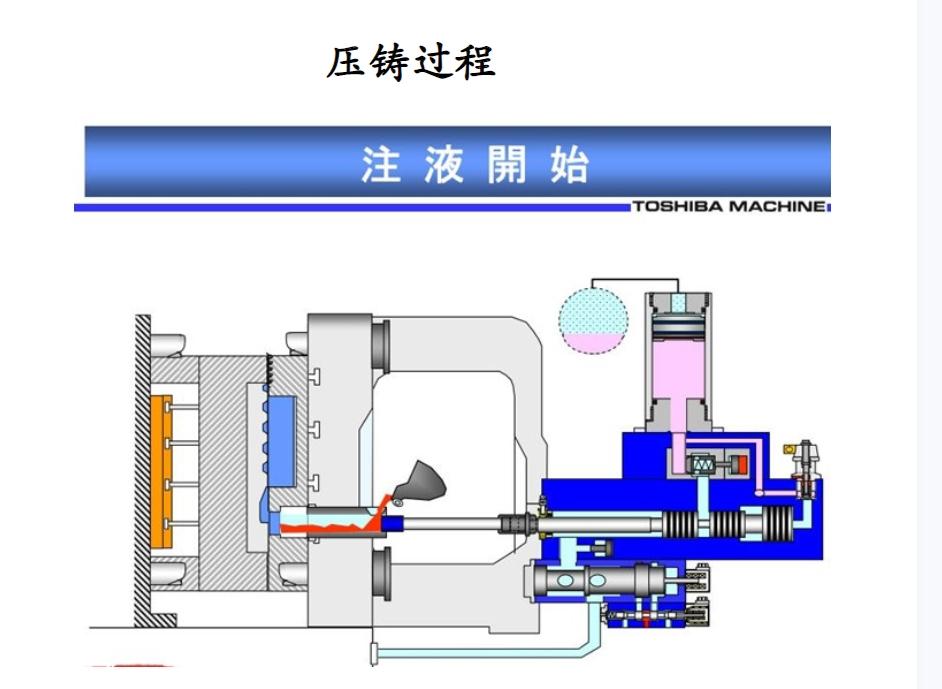
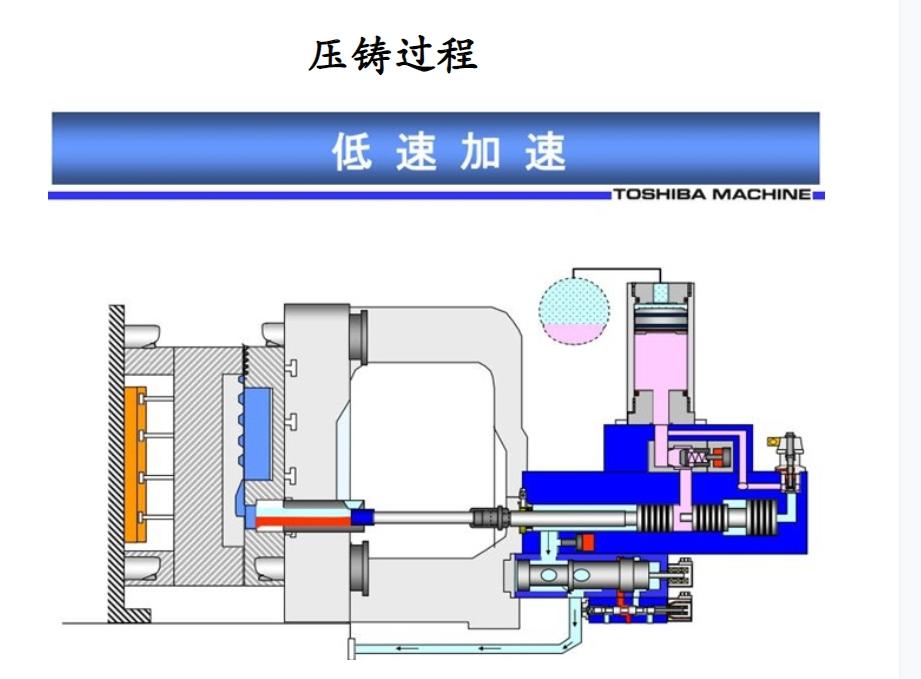
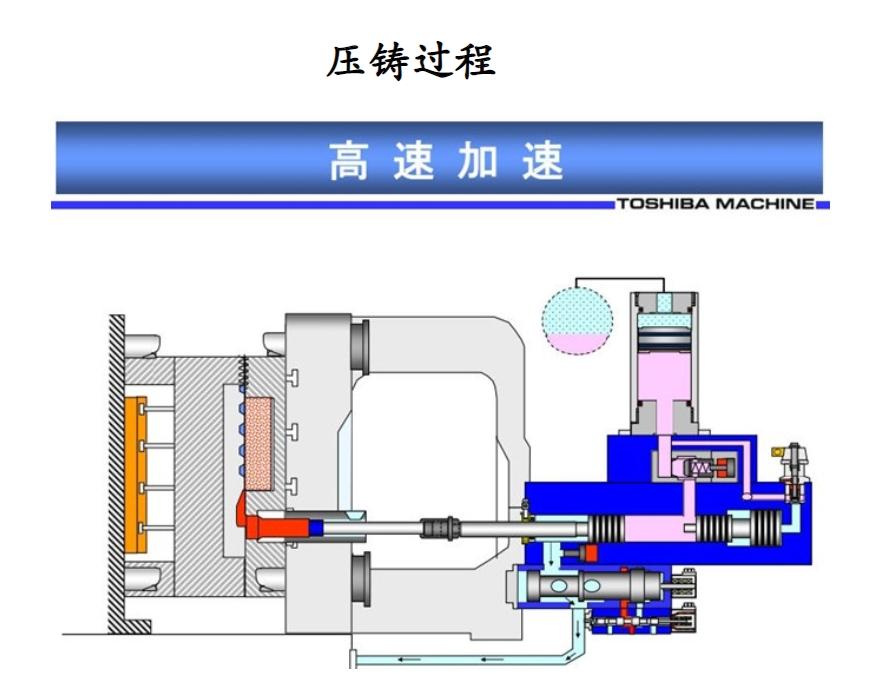
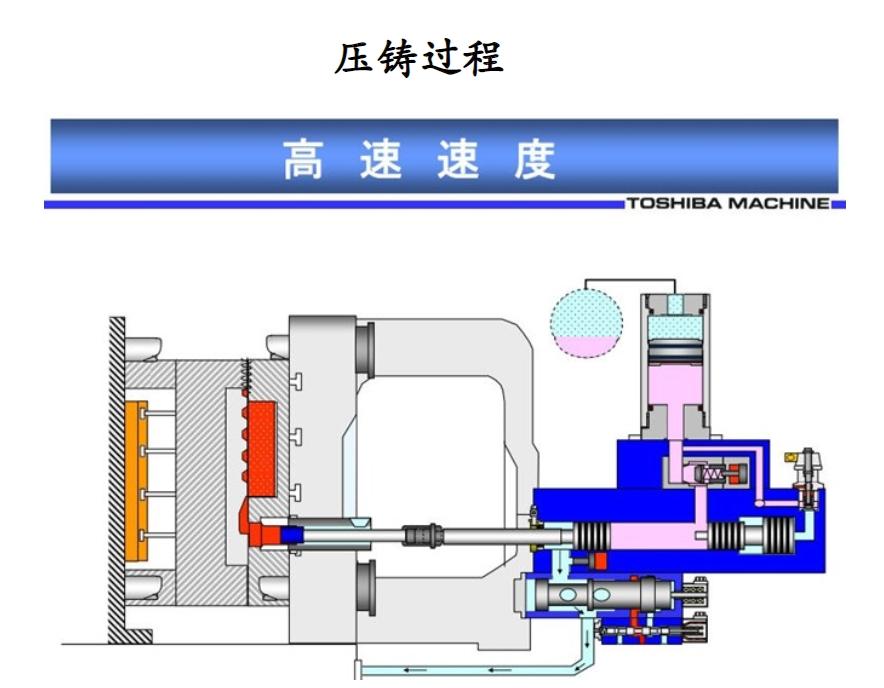
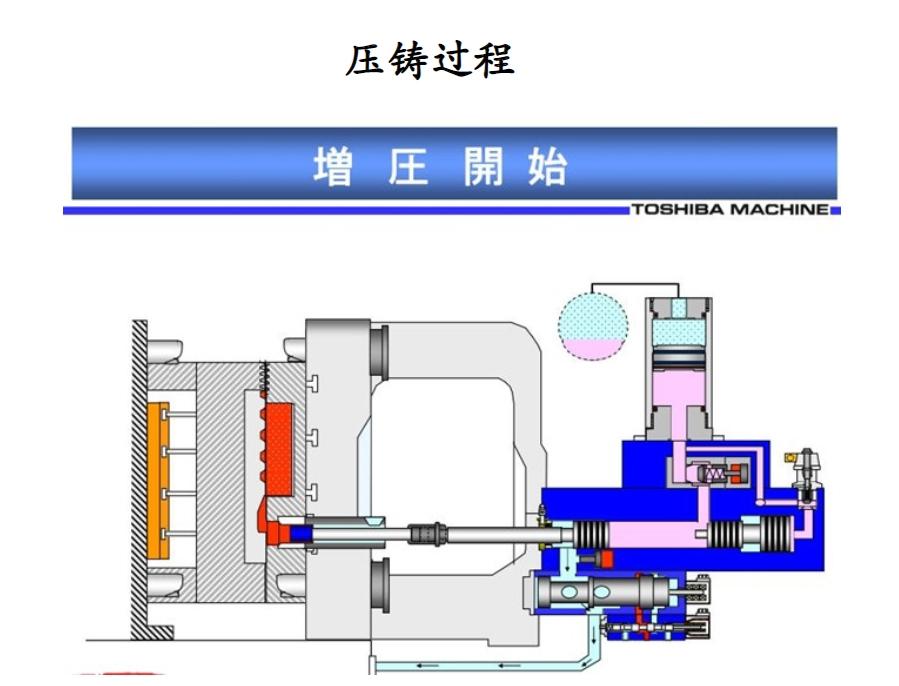
如果你学过正儿八经的金属热加工工艺,学过压铸,这段话你一定不会陌生
压铸工艺是将压铸机、压铸模、和压铸合金三大要素有机的组合而加以综合运用的过程。
压铸时金属按填充型腔的过程,是将压力、速度、温度以及时间等工艺因素得到动态平衡的过程。
这些工艺因素既相互制约,且相辅相成,只有正确选择和调整这些因素,使之协调一致,才能获得预期的结果
压铸过程中,不仅重视铸件结构的工艺性,铸型的先进性,压铸机性能和结构优良性,压铸合金选用的适应性和熔炼工艺的规范性。更应重视压力、速度、和时间等工艺参数对铸件质量的重要作用。
这段话后面会用到,这里继续讲压铸过程主要的工艺参数和关键名词
压力
压力的存在是压铸工艺区别于其他铸造方法的主要特点。压力是使铸件获得组织致密和轮廓清晰的因素
压力的表示形式有压射力和比压两种。
压射力
压射力是压铸机压射机构中推动压射活塞运动的力。压射力是反映压铸机功能的一个主要参数。
压射力的大小是由压射缸的截面积和压射腔内工作液的压力所决定。压射力的公式如下:
F压=P液XA缸
比压
压室内熔融金属在单位面积上所受的压力称为比压。比压是压射力与压室截面积的比值其计算公式如下:
P比=P射/A室
比压是熔融金属在填充过程中各阶段实际得到的作用力的大小的表示方法,反映了熔融金属在填充的各个阶段以及金属流经各个不同截面积时的力的概念。
将填充时的比压称为填充比压又称压射比压。增压阶段的比压称为增压比压这两个比压的大小同样都是根据压射力来确定的
压力的作用和影响
填充比压是克服浇注系统和型腔中的流动阻力,特别是内浇口处的阻力,使金属液流保证达到需要的内浇口速度。
增压比压则是决定了正在凝固的金属所受到的压力以及这时所形成的胀型力的大小
比压对铸件机械性能的影响 :比压增大,结晶细,细晶层增厚,由于填充特性改善,表面质量提高,气孔影响减轻,从而抗拉强度提高。
对填充条件的影响:合金熔液在高比压下填充型腔,合金温度升高,流动性改善,有利于铸件质量的提高。
速度
压铸过程中,压射速度受压力的直接影响,又与压力共同对铸件内部质量,表面要求和轮廓清晰程度起着重要的作用。压力是速度的基础
速度的表示形式分为冲头速度和内浇口速度两种
冲头速度与内交口速度的关系
根据连续性原理,在同一时间内金属流以速度V1流过压室截面积为F1的合金液体积,应等于以速度V2流过内浇口截面积为F2的合金液体积
F1室V1射=F2内V2内
因此,压射锤头的压射速度越高,则金属流经内浇口的速度越高。
压射速度
压射速度又分为两级,一级压射速度亦称慢压射速度,这级速度是指冲头起始动作直至冲头将室内的金属液送入内浇口之前的运动速度,在这一阶段中要求将压室中的金属液充满压室,在既不过多地降低合金液温度又有利于排除压室中的气体的原则下。
二级压射速度又称 快压射速度,这个速度由压铸机的特性所决定,压铸机所给定的最高压射速度一般在4-5米/秒范围内 。
快压射速度的作用和影响
快压射速度对合金机械性能的作用和影响,提高压射速度,动能转化为热能,提高了合金熔液的流动性,有利于消除流痕,冷隔等缺陷,提高了机械性能和表面质量,但速度过快时,合金熔液呈雾状和气体混合,产生严重裹包气,机械性能下降。
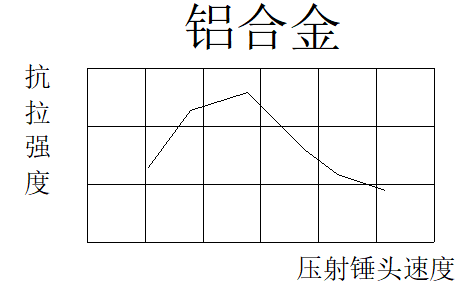
内浇口速度
熔融金属进入内浇口导入型腔时的线速度,称为内浇口速度
通常采用的内浇口速度范围为15-70米/秒。
内浇口速度高低与铸件机械性能的影响极大,内浇口速度太低,铸件强度下降;速度提高,强度上升;速度过高,强度又下降 。
后面还有温度,时间等参数没讲,考虑到小米还暂时没被造谣到这个地方,普通人还不会被误解,我本着偷懒的原则就先不讲这几个点,仅仅把他们当做可以调整的参数,方便后面理解。
前面我用塑胶模型举例子,用塑胶模型的各种瑕疵和我自己拼装时发现的问题,就是试图告诉大家哪怕一个注塑行业,他的简单产品都能有如此之多的问题,而这些问题的解决需要大量的,复杂的参数调整,技术力和研发投入,已经大量的人力物力财力砸进去,才能在注塑这个6-7000亿人民币一年的市场站稳脚跟,有无数人和你一样有钱可以买注塑机,但是只有少数工厂能交付好的产品存活下来,前面的例子就是原因。
同样的,我会通过课本和教材举例一些压铸工艺产生的不良,或者说差一些的压铸可能哪里有问题,以及问题的原因,带大家反推一下压铸工艺的复杂性。
流痕
铸件表面上呈现与金属液流动方向相一致的,用手感觉得出的局部下陷光滑纹路。
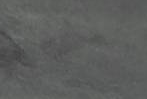
原因:两股金属流不同步充满型腔而留下的痕迹. 模具温度低,如锌合金模温低于150℃,铝合金模温低于 180℃,都易产生这类缺陷.填充速度太高,涂料用量过多
排除措施:调整内浇口截面积或位置,调整模具温度,增大溢流槽。适当调整填充速度以改变金属液填充型腔的流态。涂料适用薄而喷匀。
冷隔
温度较低的金属流互相对接但未熔合而出现的缝隙。呈现不规则的线形,有穿透的和不穿透的两种,在外力作用下有发展趋势。
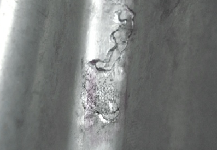
原因:金属液浇注温度低或模具温度低.合金成分不符合标准,流动性差.金属液分股填充,融合不良,浇口不合理,流程太长填充速度低或排气不良. 比压偏低.
排除措施:适当提高浇注温度和模具温度。改变合金成分,提高流动性。改进浇注系统,改善填充条件。改善排溢条件,加大溢流量。提高压射速度,改善排气条件。提高比压。
拉伤、粘模伤痕
顺着脱模方向,由于金属粘附,模具制造斜度太小而造成铸件表面的拉伤痕迹,严重时称为拉伤面。
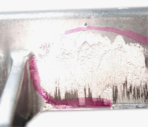
原因:型芯、型壁的铸造斜度大小或出现倒斜度。型芯、型壁有压伤痕。合金粘附模具。铸件顶出偏斜或型芯轴线偏斜。型壁表面粗糙。涂料常喷涂不到。铝合金中含铁量低于0.6%
排除措施:修正模具,保证制造斜度。打光压痕。合理设计浇注系统避免金属流对冲型芯型壁,适当降低填充速度。修正模具结构。 打光表面。涂料用量薄而均匀,不能漏喷涂料。适当增加含铁量至适当增加含铁量至0.6~0.8%。
缩孔 缩松
铸件平滑表面上出现凹瘪的部分,其表面呈自然冷却状态。
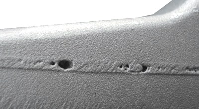
原因:模具温度太高。填充速度太高,金属液流卷入气体过多。涂料发气量大,用量过多,浇注前未燃尽,使挥发气体被包在铸件表层。排气不畅。 开模过早。合金熔炼温度过高。
排除措施:冷却模具至工作温度。降低压射速度,避免涡流包气。选用发气量小的涂料,用量薄而均匀,燃尽后合模。清理和增设溢流槽和排气道。调整留模时间。修整熔炼工艺。
气泡 鼓泡
铸件表皮下,聚集气体鼓胀所形成的泡。

原因:型芯、型壁的铸造斜度大小或出现倒斜度。型芯、型壁有压伤痕。合金粘附模具。铸件顶出偏斜或型芯轴线偏斜。型壁表面粗糙。涂料常喷涂不到。铝合金中含铁量低于0.6%
排除措施:修正模具,保证制造斜度。打光压痕。合理设计浇注系统避免金属流对冲型芯型壁,适当降低填充速度。修正模具结构。 打光表面。涂料用量薄而均匀,不能漏喷涂料。适当增加含铁量至适当增加含铁量至0.6~0.8%。
气孔
卷入压铸件内部的气体所形成的形状较为规则,表面较为光滑的空洞。
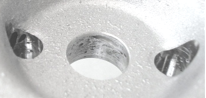
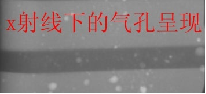
原因:主要是包卷气体引起:浇口位置选择和导流形状不当,导致金属液进入型腔产生正面撞击和产生旋涡。浇道形状设计不良。 压室充满度不够。内浇口速度太高,产生湍流. 排气不畅。模具型腔位置太深。涂料过多,填充前未燃尽。炉料不干净,精炼不良。机械加工余量太大。
排除措施:选择有利型腔内气体排除的浇口位置和导流形状,避免金属液先封闭分型面上的排溢系统。直浇道的喷嘴截面积应尽可能比内浇口截面积大。提高压室充满度,尽可能选用较小的压室并采用定量浇注。在满足成型良好条件下,增大内浇口厚度以降低填充速度。在型腔最后填充部位处开设溢流槽和排气道,并应避免溢流槽和排气道被金属液封闭。深腔处开设排气塞,采用镶拼形式增加排气。涂料用量薄而均匀,燃尽后填充,采用发气量小的涂料。炉料必须处理干净、干燥,严格遵守熔炼工艺减少机械加工余量。调整压射速度和快压射速度的转换点。降低浇注温度,增加比压。
裂纹
铸件上合金基体被破坏或断开形成细丝状的缝隙,有穿透的和不穿透的两种,有发展趋势。 裂纹可以分为冷裂纹和热裂纹两种,他们的主要区别是冷裂纹铸件开裂处金属未被氧化,热裂纹铸件开裂处金属被氧化
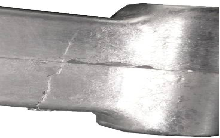
原因:铸件结构不合理,收缩收到阻碍,铸造圆角太小。抽芯及顶出装置在工作中发生偏斜,受力不均匀。模具温度低。开模及抽芯时间太迟。选用合金不当或有害杂质过高,使合金塑性下降。
排除措施:改进铸件结构,减少壁厚差,增大铸造圆角。修正模具结构。提高模具工作温度。缩短开模及抽芯时间。严格控制有害杂质,调整合金成分。
欠铸 浇不足 轮廓不清 边角残缺
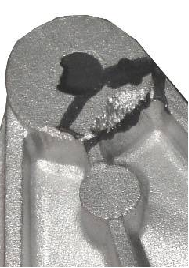
原因:(1)合金液流动不良引起: 合金液含气量高,氧化严重,以致流动性下降。合金浇注温度及模具温度过低。 内浇口速度过低。 蓄能器内氮气压力不足。压室充满度小。铸件壁太薄或厚薄悬殊等设计不当。
(2)浇注系统不良引起:浇口位置,导流方式,内浇口股数选择不当。内浇口截面积太小。 (3)排气条件不良引起:排气不畅。涂料过多,未被烘干燃尽。模具温度过高,型腔内气体压力较高,不易排出。
排除措施(1)改善合金的流动性:采用正确的熔炼工艺,排除气体及非金属夹杂物。 适当提高合金浇注温度和模具温度。提高压射速度。 补充氮气,提高有效压力。 采用定量浇注。改进铸件结构,适当调整壁厚。
(2)改进浇注系统:正确选择浇口位置和导流方式,对不良形状铸件及大铸件采用多股内浇口为有利。增大内浇口截面积或提高压射速度。
(3)改善排气条件:增设溢流槽和排气道,深凹型腔处可开设通气塞。涂料使用薄而均匀,吹干燃尽后合模。降低模具温度至工作温度。
看完前面几个不良的产生和解决方案,其实我们已经能看出问题了,
【压铸系统好像是矛盾的】
压铸过程中遇到的问题有的要靠增大压力,增大压射速度(比如欠铸,残缺)解决,有的要靠减小压力,减小压射速度(比如流痕,缩孔)解决,有的要靠提升温度解决,有的要靠降低温度解决等等,因为压铸是一整个工艺,这个工艺非常复杂,是将压铸机、压铸模、和压铸合金三大要素有机的组合而加以综合运用的过程。
而大压铸中,压铸机是一个组成部分,而大压铸的核心,是加以综合运用
看完这些,再回到这句话,是不是受益匪浅。
压铸工艺是将压铸机、压铸模、和压铸合金三大要素有机的组合而加以综合运用的过程。
压铸时金属按填充型腔的过程,是将压力、速度、温度以及时间等工艺因素得到动态平衡的过程。
这些工艺因素既相互制约,且相辅相成,只有正确选择和调整这些因素,使之协调一致,才能获得预期的结果
压铸过程中,不仅重视铸件结构的工艺性,铸型的先进性,压铸机性能和结构优良性,压铸合金选用的适应性和熔炼工艺的规范性。更应重视压力、速度、和时间等工艺参数对铸件质量的重要作用。
所以当我听到小米自研压铸岛,做的核心工作是压铸岛匹配小米汽车工厂的整个生产线,找到了中国先进材料研究所来做基础材料研发,我就知道小米团队做的是透彻的对压铸工艺的认知,是理性的评估生产需求,研发正确的,匹配自身需求的东西,并且做出了成果向所有人展示的过程。
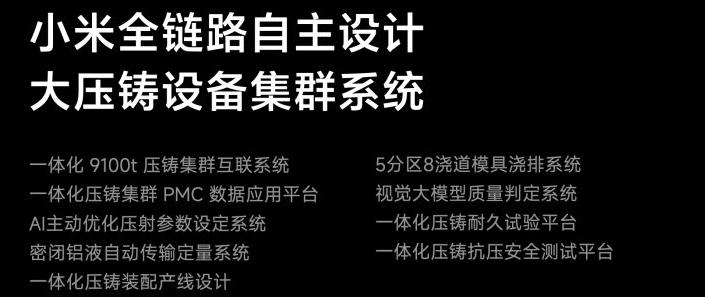
9100吨只是“压铸集群互联系统”的前置定语一笔带过。
PMC数据应用平台保证了一体化压铸集群的高效数据应用。
AI主动优化的压射参数设定代替了老师傅和玄学参数表的机械标定,通过AI辅助结合产品设计仿真标定参数。
封闭铝液自动传输定量系统保证了铝液传输过程中的纯净,减少了过程损耗,减小了压铸损失。
一体化压铸配产线设计提供了对小米整个工厂匹配的配合流水线,提升整体效率。
5分区8浇道模具浇排是世界顶级大压铸厂的水平
视觉大模型质量判定系统配合原有的CT,超声波,相对于行业人工判定提升了一致性,减少了漏报率。
一体化压铸抗压安全测试平台,让大压铸作为特种设备,在国家安全法规的基础上进一步提升安全性,为未来更高的参数和技术指标提供安全保障。
而正如前面所说
压铸工艺是将压铸机、压铸模、和压铸合金三大要素有机的组合而加以综合运用的过程。
前面很多的工艺缺陷和问题,除了压铸流程参数问题,压铸模具设计修磨省模的问题,就是压铸合金的问题,因为材料学,金相学的问题显著影响到金属热工艺的结果,调整组分会影响什么参数,会有什么样的效果,直接看下面这个链接
我直接引用
大佬关于材料学的观点,深得我意。一个认真做事的人,展示一些自己的工作成就,9100吨的锁模力只是截面积*最终压力的数值结果,但是这个参数的调整和大压铸体系的自研,代表着整套先进压铸体系的落地,他的成果就是小米发布会后面展示的
1,小米做了很强的大压铸结果,通过对大压铸全流程的掌握,减少了840个焊点,降低了2分贝噪音(这个也涉及到大量的声学和机械振动仿真),减少了17%的重量,而且已经进行了200万km的测试
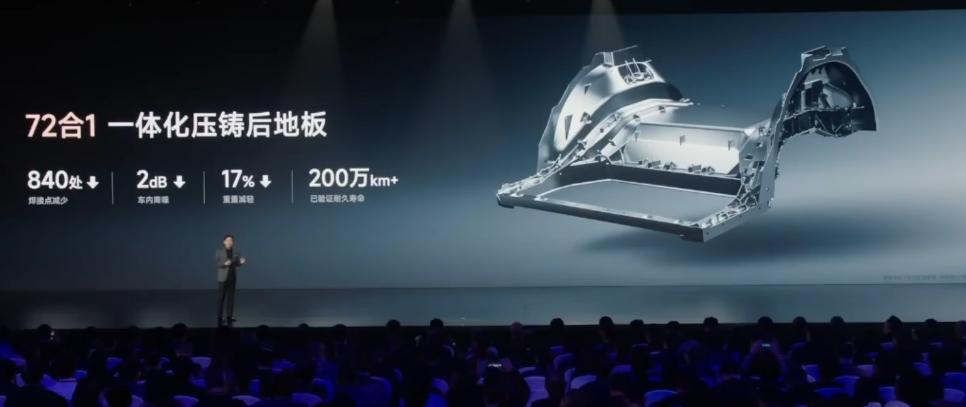
2,小米虽然有能力做超大压铸件,但是不贪图大和省钱,而是综合了用户的碰撞修复成本,整车结构强度和大压铸的成本降低,提供了三段式后地板,这样后部碰撞时大压铸可以保持完整,只有后地板溃缩区和凸起结构变形,更换这个部件即可。
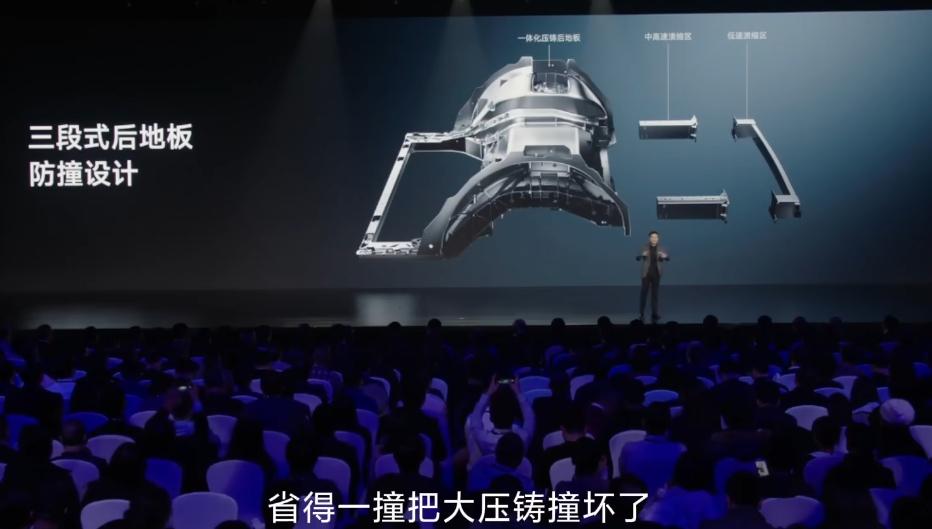
在一些人眼中,压铸技术就和玩儿童玩具一样简单,压铸机就好像是一节五号电池,装到玩具里就能立刻使用,打开开关,就能立刻源源不断的产生好的结果,而且必然是好的结果,他们的信仰也只需要买一节五号电池就能立刻启动这个小玩具。
在他们眼中,小米做的一切工作,不过是把这节五号电池的电压从1.5V变成了1.6V,还有大聪明拿出来了正态分布曲线
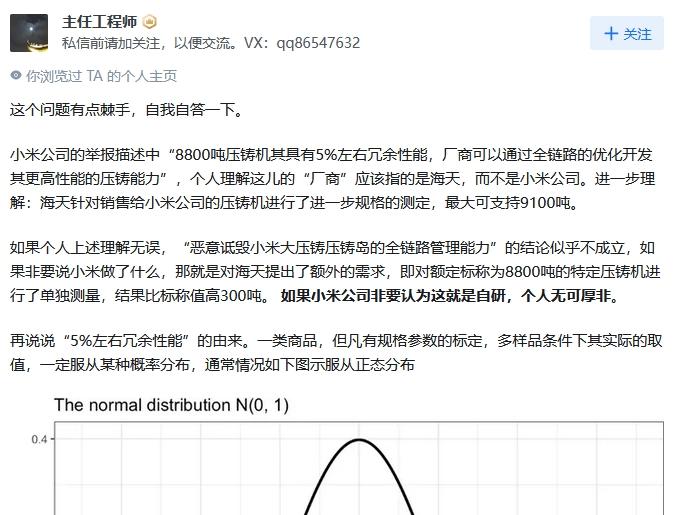
如果非要举个例子,如果大压铸是一个炖菜的餐馆,压铸机则是高压锅。
有人真的自己买高压锅,自己研究锅的参数,做食品高压炖煮的仿真,认真去做每一道菜,研究如何控制火候,如何控制时间,如何控制调味料,如何科学的利用好大模型和AI的技术优势,甚至跑到原材料前端,研究具体什么样的食材可以更好的做炖菜,并且落地到具体的工业界中来,配合已有的高压锅,完成当前团队技术下成本最低,效果最好,品质最优秀的餐馆出餐。
而有一些聪明绝顶的人,则歇斯底里的向周围人叫嚷着:这人家的高压锅是买的,竟然调高了工作压力,就敢宣布餐馆整个流程是自研的,多不要脸啊,他又吹牛了,我太懂做菜了,他做的不过是改点盐分,没什么大不了的,我的料理包代工厂也能做,料理包多好啊。
如果你想跟他讲道理,我这一篇你看完就差不多了,如果你想和他们魔法对轰,那么我认为这篇回答是极好的
另外啊,我大概知道为什么有人抓着吨位黑了,因为他们家外包压铸铸造流程,用的C611TM,屈服强度120Mpa,抗拉强度250Mpa
而小米的大压铸,用的泰坦合金(其实是一系列合金,这个大类中所有的免热处理铝合金,他们拥有不同的热加工性能,但是保持屈服强度135-170Mpa,抗拉强度270-320Mpa,断裂延伸率不超过10%,同时做到了强大的压铸结构最终结果。
你猜他们为什么只关注一个所谓的吨位,却连这个吨位来自哪里,如何计算都不知道呢?
外包压铸为什么不能配合主机厂协同设计,为什么不能用更强的免热处理铝合金,为什么不能降低2dB噪音,为什么不做大压铸和后溃缩区防护独立,是因为不想吗?
我对一些群体的评价是,绝望的文盲们。